PP/PET Strapping Band Making Machines : The Essential Reference for Packaging
PP/PET strapping band making machines are essential equipment for the packaging industry. They are used to produce strapping bands, which are used to secure a wide variety of goods, including boxes, pallets, and drums. PP/PET strapping band making extrusion machines can improve packaging efficiency, reduce costs, and enhance safety. In this blog post, we will provide a comprehensive guide to PP/PET strapping band making machines. We will discuss the components, different grades of strapping bands, applications, and buying guide of PP/PET strapping band extrusion lines.
Understanding Key Components of Strapping Band Making Machines and Choosing the Right one
The design and features of strapping roll extrusion machines can vary depending on the manufacturer and intended use. These plastic straps are commonly used in industries to package, bundle, and secure goods. The following key components are essential for the extrusion process of plastic straps :
-
Extruder:
The straps extruder is the core component responsible for melting and mixing the raw materials. It consists of a screw, barrel, temperature zone with heater bands, and cooling fans.
-
Die pack:
The die head shapes the molten plastic material into the desired strapping band. It can be designed to produce different band sizes.
-
Cooling System:
After extrusion, the plastic strapping band needs to be rapidly cooled to solidify. This is achieved by circulating water through a cooling system or heat exchanger to maintain a stable water temperature.
-
Godet Unit:
Comprised of rollers, the godet unit pulls the extruded plastic material at a consistent speed. The speed and stretching ratio will affect the final dimensions and tensile strength of the strapping band.
-
Stretching Hot Air Oven:
This is essential for maintaining the required tension in the strapping band during the extrusion process, ensuring uniform thickness and width.
-
Embossing Unit:
The embossing unit is an optional device that creates a diamond pattern on the strapping bands to improve their friction. This feature depends on customer demand.
-
Relaxing Hot Air Oven & Cooling:
This annealing system helps maintain the properties and stability of the strapping band.
-
Winding Unit:
After the extrusion process, the strapping band is wound onto spools or coils. The winding unit may include automatic tension control to ensure consistent winding.
What's the Differecnes ? Manual vs. Machine Grade Strapping Bands
There are significant differences between automatic packing and manual/semi-automatic packing when it comes to strapping bands. These differences primarily relate to their intended use, quality, and characteristics.
-
Manual/Semi-automatic Grade Strapping Bands
Intended Use:
Manual grade strapping bands are typically used for manual strapping applications where users apply the straps by hand. These bands are commonly used for bundling packages, securing items for shipping, or for various light to medium-duty applications.
Sold by Weight:
Manual grade straps are usually sold by weight (e.g., kilograms or pounds). The focus is on providing a certain quantity of material rather than specific quality standards.
Thickness and Strength:
Manual grade straps are thicker but may have lower tensile strength. They are designed to be easy to handle manually but may not withstand heavy loads or high tension.
Cost-Effective:
Manual grade strapping bands are cost-effective and are often chosen for applications where high tensile strength is not a primary concern.
-
Machine Grade Strapping Bands
Intended Use:
Machine grade strapping bands are designed for use with automated or semi-automated strapping machines. These machines provide consistent and high-speed strapping for various industrial and heavy-duty applications.
Sold by Weight:
Machine grade straps are typically sold by length (e.g., meters or feet). The emphasis is on providing a specific length of high-quality strapping material.
Thin and Strong:
Machine grade straps are generally thinner compared to manual grade straps but have much higher tensile strength. They are engineered to withstand the high tension and stress exerted by strapping machines.
Quality and Reliability:
Machine grade strapping bands undergo strict quality control measures to ensure consistent thickness, width, and strength. They are reliable for securing heavy loads during transportation.
Higher Cost:
Machine grade strapping bands are often more expensive than manual grade straps due to their superior quality and performance characteristics.
In summary, the choice between manual grade and machine grade strapping bands depends on the specific application and requirements. Manual grade straps are suitable for lighter tasks where cost-efficiency is crucial, while machine grade straps are essential for heavy-duty industrial applications where strength, consistency, and reliability are paramount. The difference in selling methods (by weight vs. by length) reflects these distinct purposes and quality standards.
For example, if a 10kg manual grade strap roll is produced by another machine, a 10kg machine grade strap produced by Plasco machine grade strapping machine will have a longer length in meters, higher quality, and much better strength. Consequently, the price for machine grade straps is certainly higher when sold by meter.
For more information on machine grade of strapping band making machines, please visit the Strapping Band Extrusion Line.
Applications of PP & PET Strapping Bands
Polypropylene (PP) and Polyethylene (PET) strapping bands have a wide range of applications in various industries due to their unique characteristics. Here are some common uses for each type of strapping band:
-
Polypropylene (PP) Strapping Bands
Light to Medium-Duty Packaging:
PP strapping bands are often used in packaging and bundling applications where the loads are relatively light or have low tensile strength. This includes items like cartons, newspapers, magazines, and other lightweight products.
Cost-Effective Bundling:
PP strapping is a cost-effective solution for bundling items together. It is commonly used in the food and beverage industry to secure multiple packages, such as beverage cartons or packs of bottled water.
Recycling Industry:
PP strapping bands are used for bundling recyclable materials such as cartons, paper, and plastics for recycling facilities.
-
Polyethylene (PET) Strapping Bands
Heavy-Duty Packaging:
PET strapping bands are known for their high tensile strength, making them suitable for heavy-duty packaging applications. They are used to secure palletized loads of heavy goods, such as construction materials, metal products, and industrial equipment.
Construction and Building Industry:
PET strapping is commonly used in the construction and building materials industry to bundle bricks, lumber, and other heavy building materials for transportation.
Transportation and Shipping:
PET strapping is widely used in the transportation and logistics industry to secure goods on pallets or in containers during transit, preventing shifting or damage.
Steel and Metal Industry:
Industries that require exceptional tensile strength, such as the steel and metal sector, prefer PET strapping for securing substantial coils, sheets, and metal products.
Factors to Consider When Choosing a Strapping Band Making Machine
When choosing a strapping band making machine, it is important to consider the following factors:
- The factory space and environment
- The size and weight of the goods to be wrapped up
- The desired strength and durability of the strapping bands
- The production capacity
- The budget for the line scale
Strapping Band Consultant Service from Plasco
Choosing the suitable strapping material (PP or PET) is a crucial step in ensuring that your application requirements are met. It is essential to consider factors such as the weight of the product being strapped and its packing grade, whether manual or automatic. Each type of strapping has its unique advantages and limitations, making it imperative to make an informed decision to ensure safe and efficient use of your products during transportation or storage. consult with our strapping band expert for advice on the best machine for your specific needs.
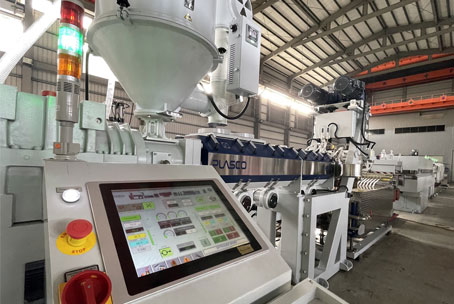
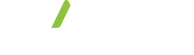
Taibao City, Chiayi County 61251, Taiwan
Phone: +886 5 2376175
E-Mail: [email protected]